Quick and Reliable Packaging Device Repair Service Solutions to Reduce Downtime
In the competitive landscape of production, the performance of packaging procedures hinges on the reliability of machinery. Quick and trustworthy repair service solutions are vital in minimizing downtime, which can lead to substantial monetary losses and functional setbacks.
Value of Timely Services
Prompt fixings of product packaging machines are crucial for keeping functional efficiency and decreasing downtime. In the hectic setting of manufacturing and product packaging, also minor breakdowns can bring about substantial hold-ups and efficiency losses. Dealing with concerns promptly guarantees that equipments operate at their optimal ability, therefore protecting the circulation of operations.
Additionally, regular and timely maintenance can protect against the escalation of small problems into significant malfunctions, which often sustain higher repair service prices and longer downtimes. An aggressive approach to machine repair not only maintains the stability of the devices however likewise improves the general dependability of the assembly line.
Furthermore, timely fixings add to the long life of product packaging equipment. Equipments that are serviced promptly are less likely to experience extreme damage, enabling businesses to optimize their financial investments. This is especially essential in markets where high-speed product packaging is important, as the requirement for regular performance is extremely important.
Benefits of Reliable Solution Service Providers
Trustworthy company play a pivotal role in making certain the smooth procedure of product packaging devices. Their know-how not only improves the effectiveness of repairs yet additionally contributes substantially to the long life of tools. Trustworthy service companies are geared up with the technical understanding and experience essential to identify issues properly and implement efficient options quickly. This minimizes the risk of repeating issues and makes certain that equipments run at optimal efficiency levels.
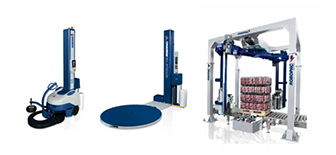
Additionally, a credible provider provides thorough support, consisting of training and advice for personnel on equipment procedure and upkeep best practices. This not only equips employees but likewise grows a culture of safety and efficiency within the company. Generally, the benefits of involving trusted provider extend past instant repairs, favorably affecting the whole functional workflow of packaging processes.
Typical Product Packaging Maker Concerns
In the realm of product packaging operations, different issues can compromise the effectiveness and performance of equipments (packaging machine repair). An additional usual problem is misalignment, which can cause jams and uneven packaging, affecting product high quality and throughput.
Electrical issues can also interfere with packaging procedures. Defective wiring or malfunctioning sensors might lead to erratic machine behavior, causing hold-ups and raised functional expenses. Furthermore, software program problems can hinder the maker's programs, bring Read Full Article about operational inadequacies.
Inconsistent product flow is an additional important issue. This can emerge from variations in product size, weight, or shape, which may influence the maker's capacity to take care of products accurately. Not enough training of operators can intensify these issues, as untrained personnel might not recognize very early indications of malfunction or might misuse the devices.
Attending to these typical packaging device concerns without delay is necessary to maintaining efficiency and ensuring a smooth procedure. Normal evaluations and positive upkeep can significantly mitigate these problems, fostering a dependable product packaging atmosphere.
Tips for Decreasing Downtime
To minimize downtime in packaging procedures, implementing a proactive upkeep method is crucial. Regularly arranged maintenance checks can recognize possible concerns before they rise, making certain makers operate effectively. Establishing a regimen that consists of lubrication, calibration, and examination of critical elements can considerably decrease the regularity of unforeseen break downs.
Training team to operate equipment properly and recognize early warning indications of breakdown can additionally play an important function. Encouraging operators with the understanding to do fundamental troubleshooting can protect against minor problems from triggering major delays. Keeping an efficient stock of vital extra parts can expedite repair services, as waiting for components can lead to extensive downtime.
Additionally, documenting equipment efficiency and upkeep tasks can help recognize patterns and reoccurring issues, enabling targeted interventions. Integrating sophisticated monitoring technologies can give real-time information, enabling predictive maintenance and minimizing the threat of abrupt failings.
Finally, promoting open communication between drivers and maintenance groups makes sure that any irregularities are without delay reported and addressed. By taking these aggressive procedures, services can boost functional effectiveness and substantially decrease downtime in packaging procedures.
Choosing the Right Repair Work Solution
Selecting the proper repair solution for check over here packaging machines is a crucial choice that can significantly affect operational effectiveness. An appropriate company ensures that your machinery is fixed quickly, efficiently, and to the greatest criteria. Begin by examining the copyright's experience with your specific kind of packaging devices. A professional familiar with your machinery can identify issues more accurately and carry out services much more swiftly.
Next, think about the company's track record. Looking for comments from other organizations within your sector can provide understandings right into dependability and top quality. Qualifications and partnerships with acknowledged devices suppliers can likewise suggest a commitment to quality.
Furthermore, examine their feedback time and schedule. A company who can use prompt support reduces downtime and keeps manufacturing circulation Going Here steady. It's additionally essential to ask about guarantee and service warranties, which can reflect the self-confidence the supplier has in their job.
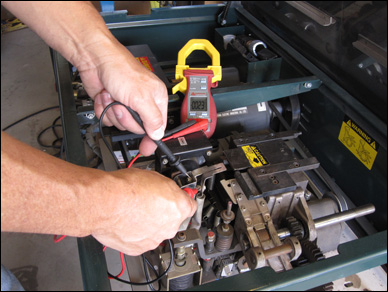
Final Thought
To conclude, the importance of fast and reliable packaging machine repair work services can not be overstated, as they play an essential role in decreasing downtime and making sure operational effectiveness. By prioritizing prompt repairs and picking reputable service suppliers, companies can effectively maintain and attend to usual issues efficiency. Applying proactive maintenance methods and purchasing personnel training additional enhances the longevity of packaging equipment. Eventually, a tactical strategy to fix solutions fosters a more resistant manufacturing setting.
Prompt repairs of packaging makers are important for preserving functional performance and lessening downtime.Additionally, timely repair services contribute to the durability of packaging machinery. In general, the advantages of involving trustworthy service carriers extend beyond immediate fixings, positively affecting the whole functional operations of product packaging processes.
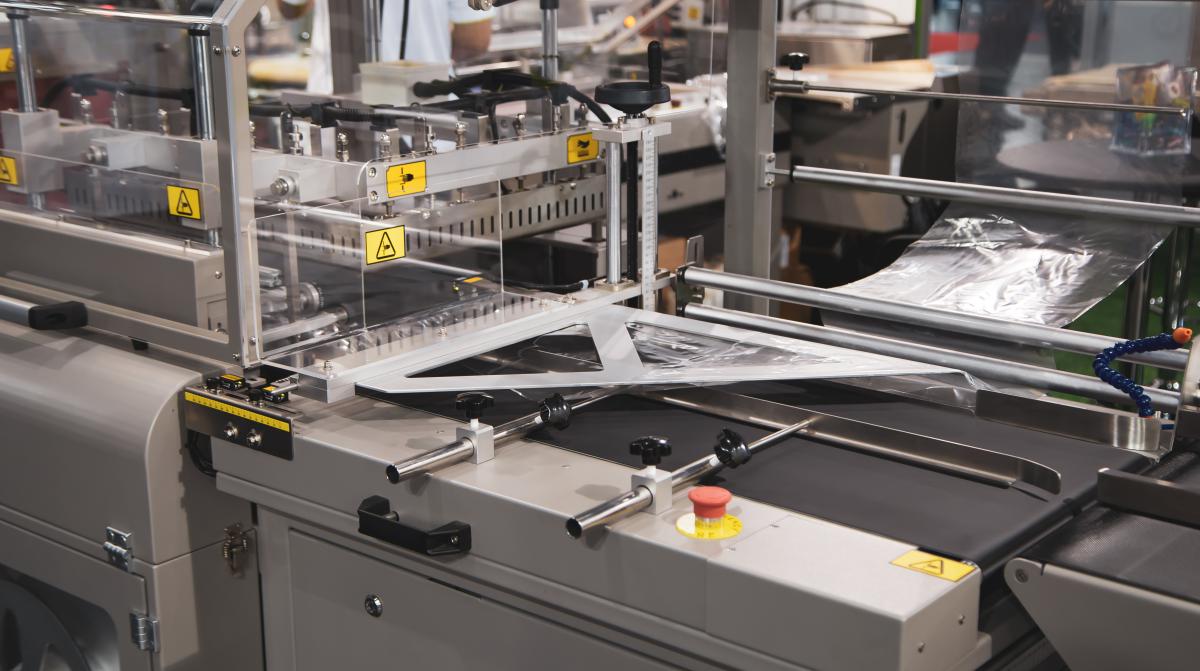